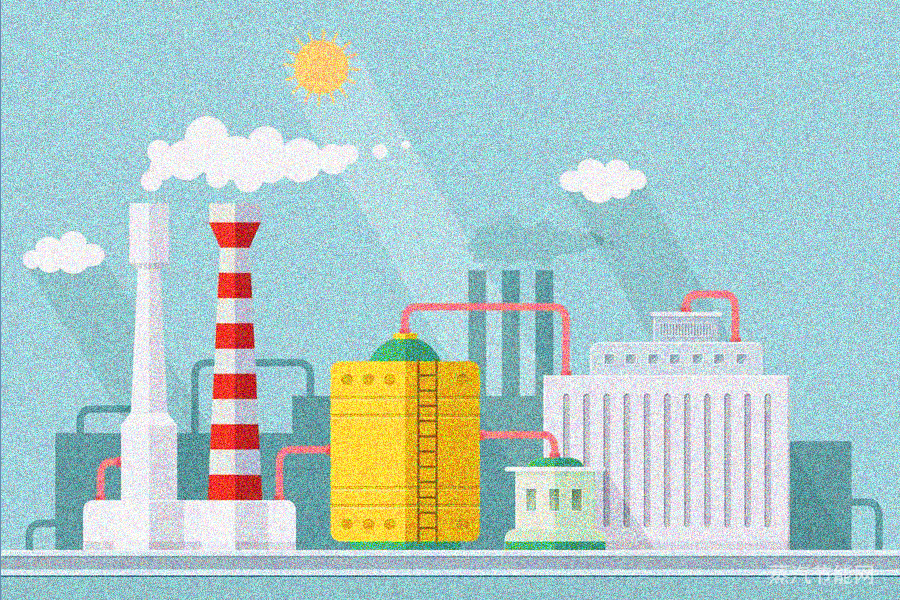
一、基本情况
现代煤化工是推动煤炭清洁高效利用的有效途径,对拓展化工原料来源具有积极作用,已成为石油化工行业的重要补充。本实施指南所指现代煤化工行业包括煤制甲醇、煤制烯烃和煤制乙二醇。现代煤化工行业先进与落后产能并存,企业能效差异显著。用能主要存在余热利用不足、过程热集成水平偏低、耗汽/耗电设备能效偏低等问题,节能降碳改造升级潜力较大。根据《高耗能行业重点领域能效标杆水平和基准水平(2021年版)》,以褐煤为原料的煤制甲醇能效标杆水平为 1550 千克标准煤/吨,基准水平为 2000 千克标准煤/吨;以烟煤为原料的煤制甲醇能效标杆水平为 1400 千克标准煤/吨,基准水平为 1800 千克标准煤/吨;以无烟煤为原料的煤制甲醇能效标杆水平为 1250 千克标煤/吨,基准水平为 1600 千克标煤/吨。煤制烯烃(MTO 路线)能效标杆水平为 2800 千克标煤/吨,基准水平为 3300 千克标煤/吨。煤制乙二醇能效标杆水平为 1000 千克标煤/吨,基准水平为1350 千克标煤/吨。截至 2020 年底,我国煤制甲醇行业能效优于标杆水平的产能约占 15%,能效低于基准水平的产能约占 25%。煤制烯烃行业能效优于标杆水平的产能约占 48%,且全部产能高于基准水平。煤制乙二醇行业能效优于标杆水平的产能约占20%,能效低于基准水平的产能约占 40%。
二、工作方向
(一)加强前沿技术开发应用,培育标杆示范企业。加快研发高性能复合新型催化剂。推动自主化成套大型空分、大型空压增压机、大型煤气化炉示范应用。推动合成气一步法制烯烃、绿氢与煤化工项目耦合等前沿技术开发应用。
(二)加快成熟工艺普及推广,有序推动改造升级。
1.绿色技术工艺。加快大型先进煤气化、半/全废锅流程气化、合成气联产联供、高效合成气净化、高效甲醇合成、节能型甲醇精馏、新一代甲醇制烯烃、高效草酸酯合成及乙二醇加氢等技术开发应用。推动一氧化碳等温变换技术应用。
2.重大节能装备。加快高效煤气化炉、合成反应器、高效精馏系统、智能控制系统、高效降膜蒸发技术等装备研发应用。采用高效压缩机、变压器等高效节能设备进行设备更新改造。
3.能量系统优化。采用热泵、热夹点、热联合等技术,优化全厂热能供需匹配,实现能量梯级利用。
4.余热余压利用。根据工艺余热品位的不同,在满足工艺装置要求的前提下,分别用于副产蒸汽、加热锅炉给水或预热脱盐水和补充水、有机朗肯循环发电,使能量供需和品位相匹配。
5.公辅设施改造。根据适用场合选用各种新型、高效、低压降换热器,提高换热效率。选用高效机泵和高效节能电机,提高设备效率。
6.废物综合利用。依托项目周边二氧化碳利用和封存条件,因地制宜开展变换等重点工艺环节高浓度二氧化碳捕集、利用及封存试点。推动二氧化碳生产甲醇、可降解塑料、碳酸二甲酯等产品。加强灰、渣资源化综合利用。
7.全过程精细化管控。强化现有工艺和设备运行维护,加强煤化工企业全过程精细化管控,减少非计划启停车,确保连续稳定高效运行。
(三)严格政策约束,淘汰落后低效产能。
严格执行节能、环保、质量、安全技术等相关法律法规和《产业结构调整指导目录》等政策,对能效水平在基准值以下,且无法通过节能改造达到基准值以上的煤化工产能,加快淘汰退出。
三、工作目标
到 2025 年,煤制甲醇、煤制烯烃、煤制乙二醇行业达到能效标杆水平以上产能比例分别达到 30%、50%、30%,基准水平以下产能基本清零,行业节能降碳效果显著,绿色低碳发展能力大幅提高。
文章来源:国家发改委